Supply Chain and Logistics
Online Training and Coaching
Get a solid understanding of supply chain fundamentals in a highly accessible and affordable program.
What’s Inside
35+ years of Supply Chain and Logistics experience all packed up to just the essential things you need to know to boost your knowledge. With this step-by-step practical information, you’ll make massive savings in your business and enhance your career prospects.
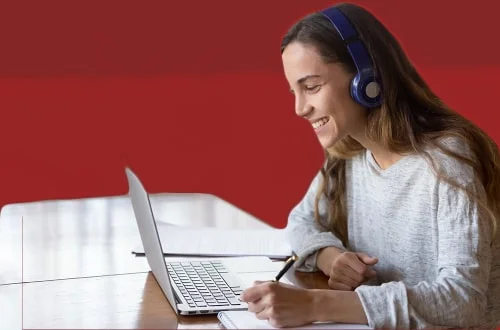
Online Classes
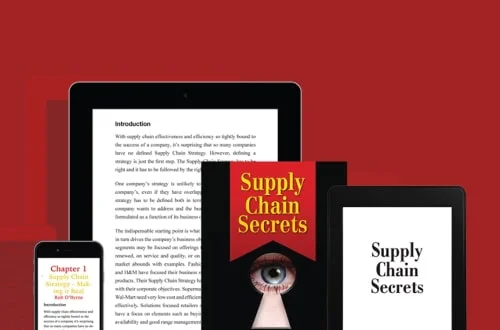
eBooks
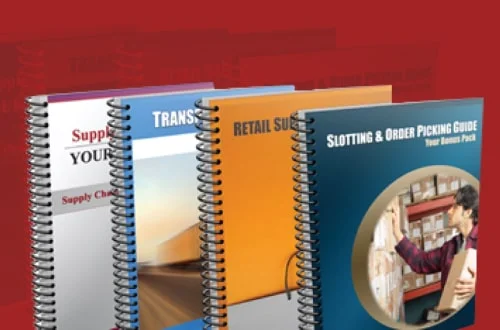
Guides
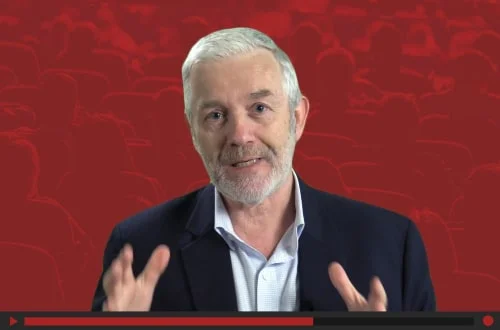
Webinars
Supply Chain Secrets is Designed to
- Help you understand the Supply Chain and Logistics jargon and concepts you come across, so you sound like an expert!
- Give you the Supply Chain knowledge that you really need.
- Give you the ‘right’ knowledge.
- Boost your respect and credibility as a business person.
- Hand you the right information, fast!
- Provide the knowledge in Supply Chain and Logistics that will help your career and income potential.
Our Founder
Do you recognise the need for supply chain knowledge and understanding? Do you just want the ‘good stuff’ quickly so that you can start using it? Well, you’re at the right place!
I’ve put this website together to help guide you achieve one or both of these goals:
- How to gain the right Supply Chain and Logistics knowledge to be much more valuable at work, and
- How to focus in like a heat seeking missile on the key Supply Chain and Logistics components that make the greatest difference to a business.
Rob O’Byrne
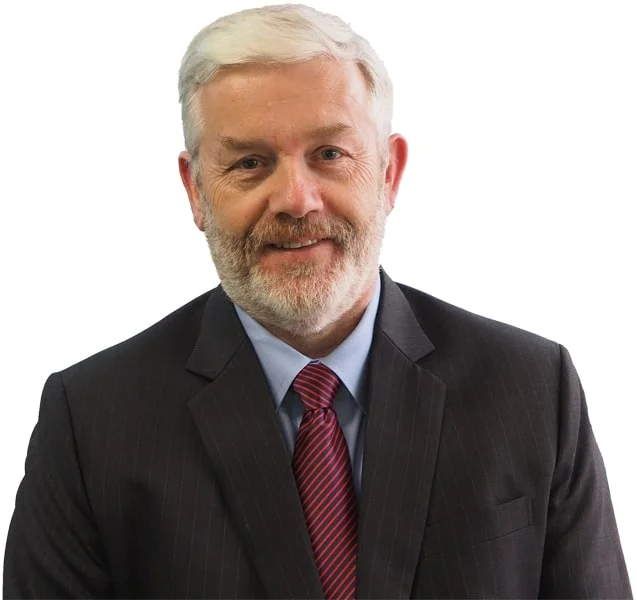
Recent Blog Posts
Network Design and Optimisation – A User Perspective
Ever wondered why some organizations succeed while others struggle with their supply chains? In fact, many organizations mess up their supply chains with the wrong networks. That's why it's crucial to learn to optimise your network design. You might ask, what benefits...
Supply Chain Challenges in the Next 5 Years with Maria Villablanca
Over time, the supply chain has experienced significant growth and continuous improvement. Have you ever pondered the trajectory of the supply chain, especially given the rapid pace of change and innovation in today's world? What challenges might lie ahead for the...
Warehouse FAILS – Common Warehouse Management Problems and Solutions
We've experienced a significant increase in demand here at Logistics Bureau for assistance in improving warehouse performance. Below, we share some of the main warehousing management problems we are helping with. Additionally, we provide simple warehouse solutions and...